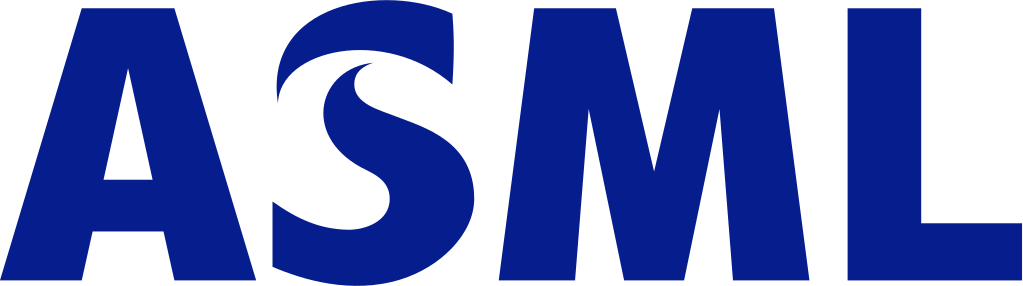
Manufacturing - Lean Expert - Linkou
ASML
- Linkou, New Taipei City
- Permanent
- Full-time
- Lead the culture change to a lean culture within Linkou factory towards sustainable improvement, aiming at an overall breakthrough on cost effectiveness and wastes elimination.
- Responsible to work on hands-on improvement projects (A3, 4C, break-through initiatives) from identifying opportunities through utilizing/implementing lean methods and to visualizing benefits.
- Deliver fact-based and structured communications to provide improvement project teams with support through lean activities planning, execution and follow-ups on lean deployment to drive continuous improvement of standards and way of working.
- Provide training and coaching of lean principles and continuous improvement methodologies to employees, including leadership teams, to build up lean culture and capabilities.
- Responsible to work with global teams on projects and performance reporting by face-to-face and teleconferences in English.
- Conduct gemba walks and regular lean maturity assessments to advance operational excellence up to the next level.
- Participate in strategic planning of lean deployment roadmap of Linkou factory.
- Other assignments from management.
- Bachelor or above.
- Major in Industrial Engineering, Statistics, Engineering or Management related fields
- 8+ years working experience with hands-on and management in Lean, Six Sigma or Continuous Improvement categories
- Experience in factory operations and semiconductor industry is a plus
- Project leadership, project management/facilitation skills, and good command of continuous improvement methodologies and quality management (for example, Lean, Six Sigma, DFSS, QCC/Kaizen, Tiered Process, TQM, ISO etc.)
- Good team player able to influence without power
- Courageous to challenge and proactively to give and seek constructive feedback
- Communication skills at all levels
- Good training and project coaching skills
- Financial acumen for project benefits and cost analysis
- Able to give presentations fluently in English and Mandarin
- Green Belt or Black Belt certification around Lean and/or Six Sigma field is preferred
- Application of Power BI is a plus
- This position reports to Lean and Business Process Improvement Manager in Operational Excellence department
- Proactive and can-do mindset is key to successfully implement Lean across functions and at all levels for operational excellence in safety, quality, service, cost and people engagement, and to create value for customers up to the next level